Services > Compression Molding and Vacuum Forming
Compression Molding and Vacuum Forming
Both our compression molding and vacuum forming are done using thermoforming, a process by which fibrous and flexible materials are molded into specific shapes using custom forms and heat. It’s a great alternative to transfer and injection molding methods as it’s more cost-efficient. It’s also ideal for parts made with more expensive materials due to reduced waste.
APPLICATIONS
• Hood Insulators
• Engine Under Covers
• Dash Insulators
• Tunnel Insulators
• Heat Shields
• Battery Boxes
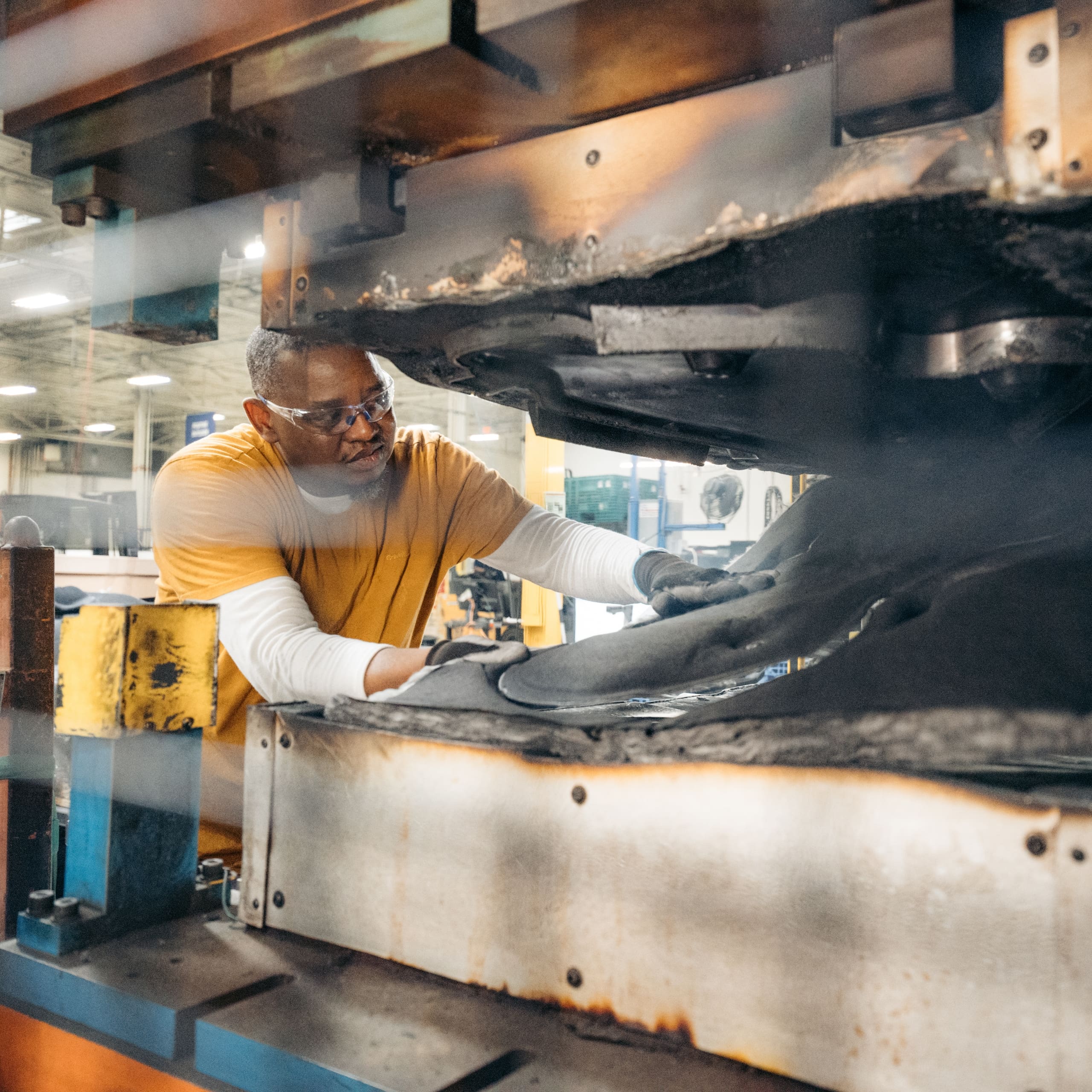
APPLICATIONS
• Hood Insulators
• Engine Under Covers
• Dash Insulators
• Tunnel Insulators
• Heat Shields
• Battery Boxes
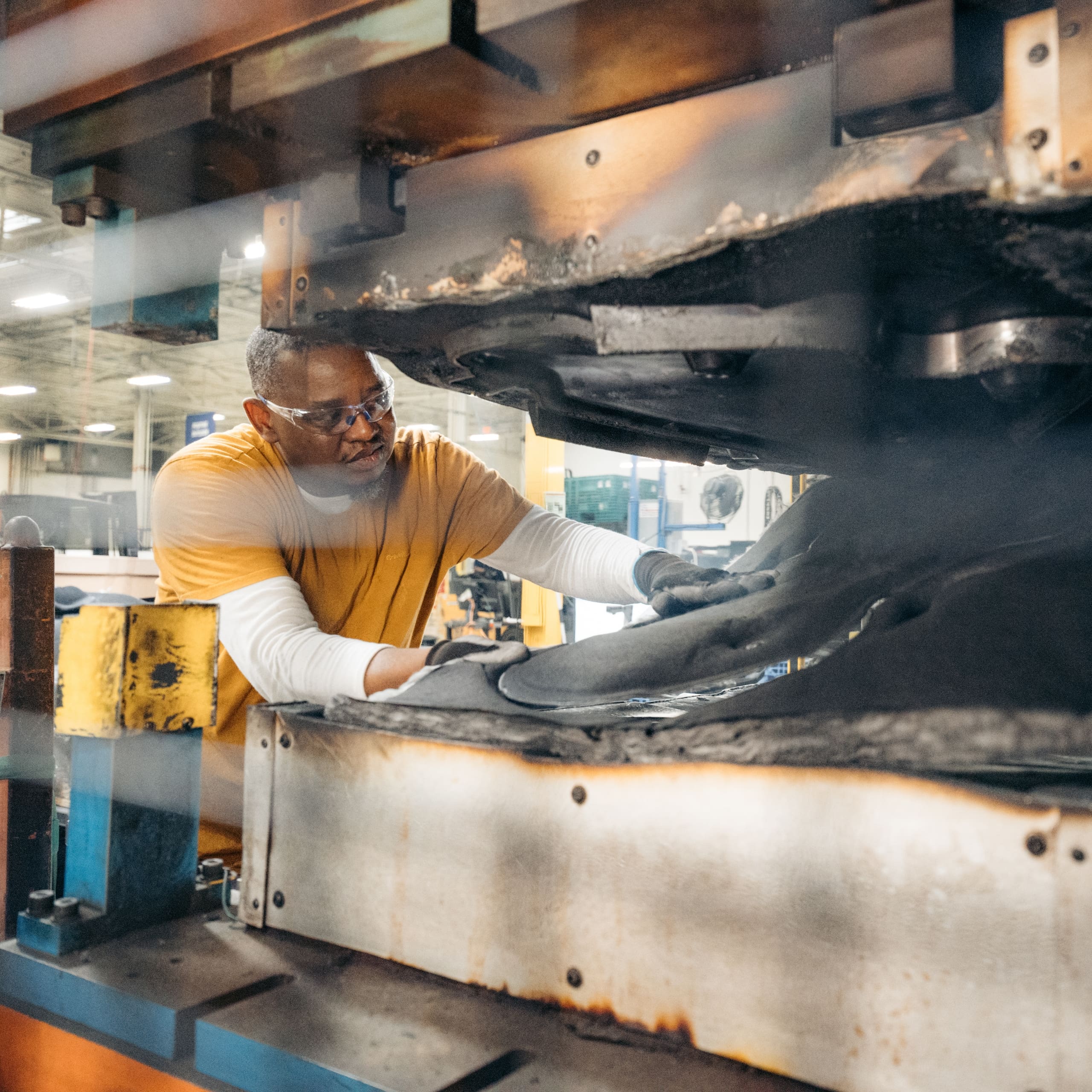
Compression Molding
Our compression molding machines allow us to quickly and efficiently produce fibrous and fiberglass parts with a high level of detail and very little material waste. This is ideal for producing larger parts, more intricate designs, and higher volume runs.
We offer a variety of base materials and Scrim options for high-heat acoustical applications that provide:
• Weight Reduction
• NVH Improvement
• V0 Flammability Requirements
• Aesthetic Appearance
• Competitive Costing
• No Post Trim or Waterjet
• Glassfiber
• PUR Foam
• PET Nonwoven
In-Process Trim
Our in-process trim process includes high tonnage, large platen/part size, efficient material, inline material indexing, and one-step tooling design avoiding the need for post-part trimming.
We offer:
• Hood Insulators
• Dash Insulators
• Tunnel Insulators
• Under Floor
• Engine Under Cover
• Alum Heat Shields
• Glasswool
• PUR Foam
• PET Fiber
Waterjet Post Trim
Our waterjet post-trim options provide multi-layer cutting, EVA processing, inline material indexing, and competitive tooling costs.
Our products include:
• Alum Heat Shields
• Glasswool Fiber
• PET Nonwoven
• Undercovers
• Tunnel Insulators
• Dash Insulators
Vacuum Forming
Industrial vacuum forming works by stretching material over a mold and using vacuum-induced pressure to shape the material to the mold. Our vacuum-forming equipment creates both large and small components out of thermoplastics. Once a mold is produced, full-scale production runs and prototype parts can be made quickly and easily for testing purposes.